The HaiQu Newsletter
Take Action to Go Beyond Compliance
Take Action to Go Beyond Compliance
Quality systems can truly shine when you're equipped with the right tools and techniques to incrementally build quality into the very design of your processes.
Join me
as we take a few minutes to explore, design, test and improve the critical systems we use in our regulated facilities. I'll help you learn how to:
Front-load effort to
increase quality
and
reduce day-to-day running costs
Design and build high quality, reliable spreadsheets that can be compliant while also
simple to validate
Evaluate, source and configure software that
does what you actually need
,
reducing the risk of big purchasing mistakes
and
increasing the usefulness, reliability, and compliance of your regulated software
Use computerized systems validation (CSV) to provide value beyond simply satisfying a regulatory checkbox.
Design workflows, SOPs, and forms that improve data integrity, simplify compliance and increase operating performance
Subscribe to the HaiQu newsletter!
Join me on the HaiQu newsletter as we take a few minutes to explore, design, test and improve the critical systems we use in our regulated facilities. From spreadsheets and software to SOPs and forms and beyond.
We'll never share your email. Unsubscribe any time.
Is Compliance the main focus of your Quality Program?
Is
Compliance
the main focus of your Quality Program?

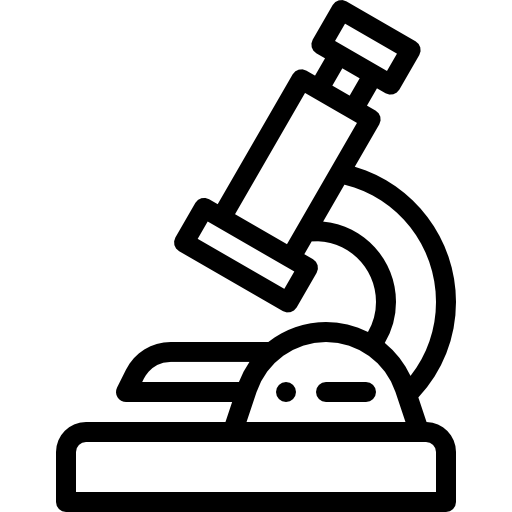
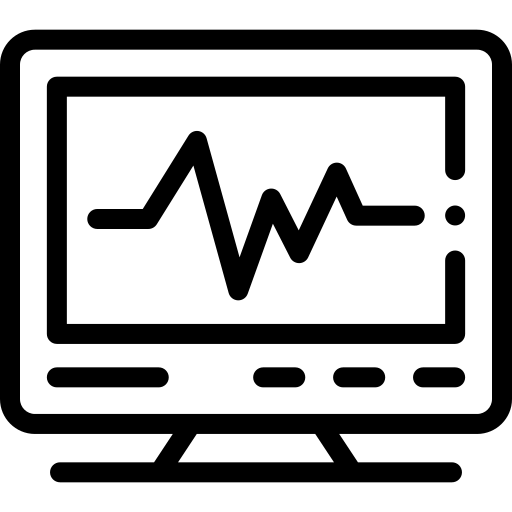
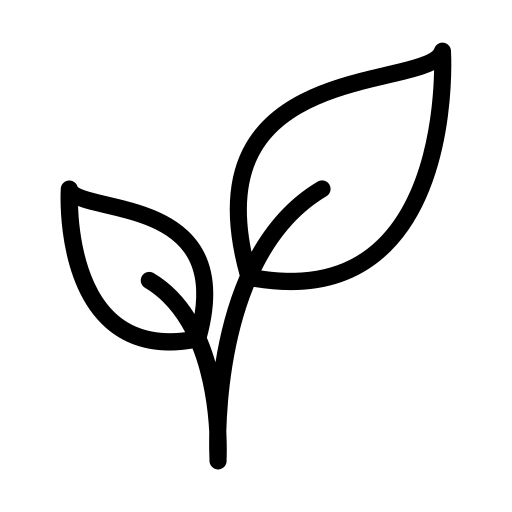
Whether your product is a pharmaceutical drug, pre-clinical safety study, a medical device or a recreational cannabis drink, you probably have a quality system in place. And most likely it was put there for one main reason: to meet stringent regulatory requirements.
At least that's the default starting point for most companies. And it's understandable why – in the beginning you often need to get up and running fast.
Does any of this sound familiar?
"Buy some templates and get the required SOPs and checklists in place as quickly as possible!"
"Record every signature and data point that could possibly be asked for in an audit!"
"Queue up
all the things
for validation!
"Don't worry, we'll use our change control program to fix it later."
But isn't compliance necessary?
But isn't compliance necessary?
Don't get me wrong, regulatory compliance is a
very
important business goal. If you ignored it you probably wouldn't be in business for very long!
But compliance is just
one input
to the design of your quality processes. And to build your quality processes for compliance's sake alone can create problems.
Problems that you can see in your day-to-day operations. For example:
Do you have SOPs that have high rates of deviations? Forms that no-one fills in correctly?
Do batch reviews / data audits add too much time between production and release?
Are you constantly playing catch-up with your change controls, deviations and CAPAs, or your validation program?
Are you stuck with clunky processes that aren't evolving or improving, but no-one wants to make changes for fear of non-compliance?
If you answered yes to any of the above, then you're not alone.
By focusing so much on compliance at design time and then only making changes as problems come up, it's easy to end up with unwieldy processes and reams of paperwork that does nothing for you but wait for the next audit.
A Quality Program isn't about Compliance... It's about Quality!
A Quality Program isn't about
Compliance
... It's about
Quality
!
Here's the thing: the usual quality system components like SOPs, data collection forms, master batch records, document control systems, change control, validation, CAPAs, Risk Analysis
were not invented to satisfy the various regulatory bodies
!
They are first and foremost
business tools
that professionals like engineers, operations managers, CEOs and quality assurance specialists have have used for decades to design, build, maintain and improve efficient, high quality production systems everywhere.
Furthermore, quality doesn't just mean the quality of your product: it's also about the quality of your records, your data, your production process, your teams, and your company as a whole.
Ok. Sounds big. Where do we start?
Ok. Sounds big. Where do we start?
We start where the interesting things happen: at the
edges
. If we look at the boundaries between the components of a complex system: for example where humans meet instruments and equipment; where records are created; where data or product is evaluated; where changes are introduced; we will find many opportunities for small improvements that yield big returns.
This newsletter will teach you simple things that can result in big improvements in product quality, data integrity and process efficiency.
I hope you'll find it useful, and if you ever want to discuss any of the topics I write about, just reply to the email.
I'm here on the other end. No robots.
At least I
think
I'm not a robot...